For plastic parts
- LUX
- For plastic parts
Our products are mainly manufactured by plastic injection moulding technology, where thanks to our intellectual and technical capabilities we can maximize the added values: special vehicle parts, the production of which requires special technology and exceptional creativity.
We produce 400 different products from plastic injection moulded parts for our customers.
We have 30 years of plastic expertise. We practice complete process control: from the idea to transport, we keep the process in hand.
We process thermoplastics by plastic injection moulding.
Injection moulding process
During injection moulding, the machine shoots the melted plastic granulate into a metal mould under high pressure, then cools the melt in the mould in a few seconds (depending on the given parameters), and when the mould is opened, the solidified product is separated from the surface and thrown away. Depending on the product, the robot places it on the conveyor belt for inspection and further work, or requiring additional cooling from the conveyor belt, it is delivered to cold water.
In our plastic injection moulding producing area, we work with Arburg and Engel type armored screw and cylinder machines. They are suitable for processing glass fiber reinforced, high strength granules.
We currently operate 20 injection moulding machines with a clamping force of which is between 15 tonnes and 600 tonnes, and their volume capacity: 10 cm3 - 2500 cm3. This can range from the smallest patents and cable end caps to larger trailer mudguards and vehicle roof window frames.
We work with about 25 types of plastic raw materials, but if you still can not find the desired raw material, our specialists will test the components that match the given product.
Our most commonly used plastic raw materials are the following:
– polyamides with glass fiber filling
– soft coloured PVC,
– polyoxymethylene POM,
– PBT, PC with glass fiber filling,
– PP polypropylene.
In addition, we can provide finished products with graphic printing, which are made using printing technology. In our printing department, we work with 10 pcs GTO type tampon printing machines, with which we can even put logos, labels and figures on our products. We can customize the machines according to individual needs, depending on the speed and complexity of the print.
From metal to plastic
One of our main aims is to make vehicles lighter by redesigning metal parts for plastic and testing sufficiently stable raw materials. In order to reduce costs and weight, we prioritize the standard of the traffic control, according to e.g. trailers and towing vehicles may not exceed a certain weight. We would like to emphasize the great stability of plastics and make our partners and customers aware that the plastic products we manufacture are durable and solid.
Production of plastic parts and fittings:
-
metal bearings moulded together with rollers,
-
towbar lock made by plastic and metal parts,
-
thermosetting „bakelite” hydraulic brake piston,
-
plastic parts containing metal inserts (copper nut (insert), sleeves, pins),
-
plastics moulded into metal parts (handles, grips, ...)
-
rollers made of two or more materials moulded together with plastic plain bearing,
-
bellows (e.g. for switch head for an overrun braking system),
-
loaded supporting pillars, consoles,
-
gear wheels,
-
trapezoidal thread lifting spindles, nuts.
We have no sources of environmental pollution, that is we have no pollutants released into the environment.
We process qualified recycled material:
-
more than 250 tons of polypropylene,
-
more than 30 tons of polyamide,
-
more than 30 tons of black soft PVC.
We possess own plastic raw material recycling company: Sunplast Ltd.
-
With own extruder, own grinders.
-
Polypropylene, polyethylene are remelted from grinds, readded with improvers, based on our own recipes. Regranulate and homogenize the materials.
-
Our capacity: 200 kg/hour.
-
At present, we produce annually approx. 800 tons of new granules.
If you would like to be an idea’s owner of a newly developed product, contact us.We design, produce and monitor all stages of it.
Our company is organized in such a way that raw material suppliers and primary partner companies can be found near our location. Working as a group, such as plastic recycling, thermosetting rubber and silicone manufacturer, rubber base mixture manufacturer and finally the thermoplastic processing company (Lux Ltd.). With this position we can fulfill plastic and rubber needs locally within a professional circle.
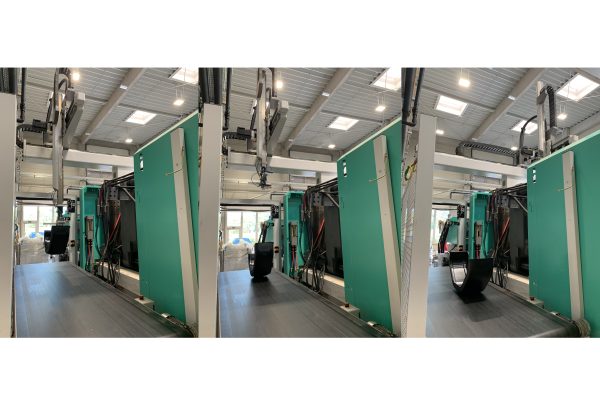

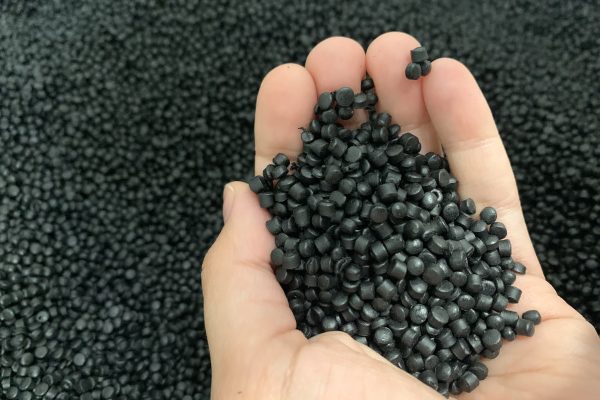
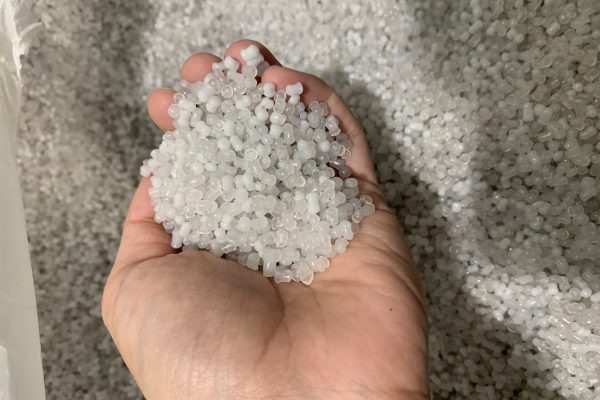
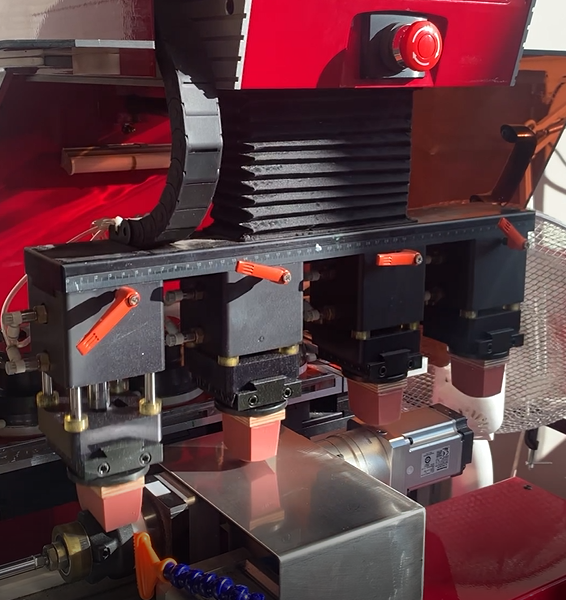